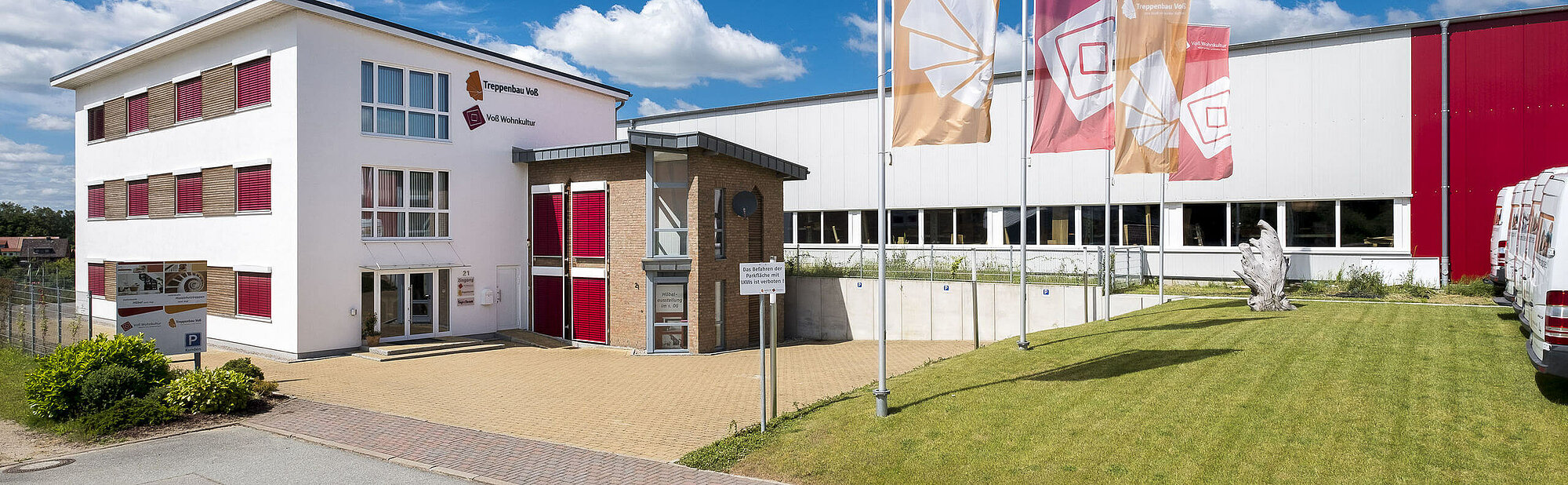
© Treppenbau Voß GmbH & Co. KG
Treppenbau Voß GmbH & Co. KG from northern Germany is producing several thousand staircases with 5 designers and 3 CNC processing centers annually. For more than two decades, the company has been relying on Compass Software’s staircase construction software. Since December 2018, the staircase builder has been utilising the new Plate Optimisation Module 2.0 that the software provider offers. Plate Optimisation 2.0 promises optimal utilisation of materials with minimal waste.
The system calculates the ideal arrangement on the plate to achieve the least amount of residual material. Plates are utilised to the max. Additionally, the program includes a clear warehouse management tool and left-over plates are automatically re-used and added back into stock.
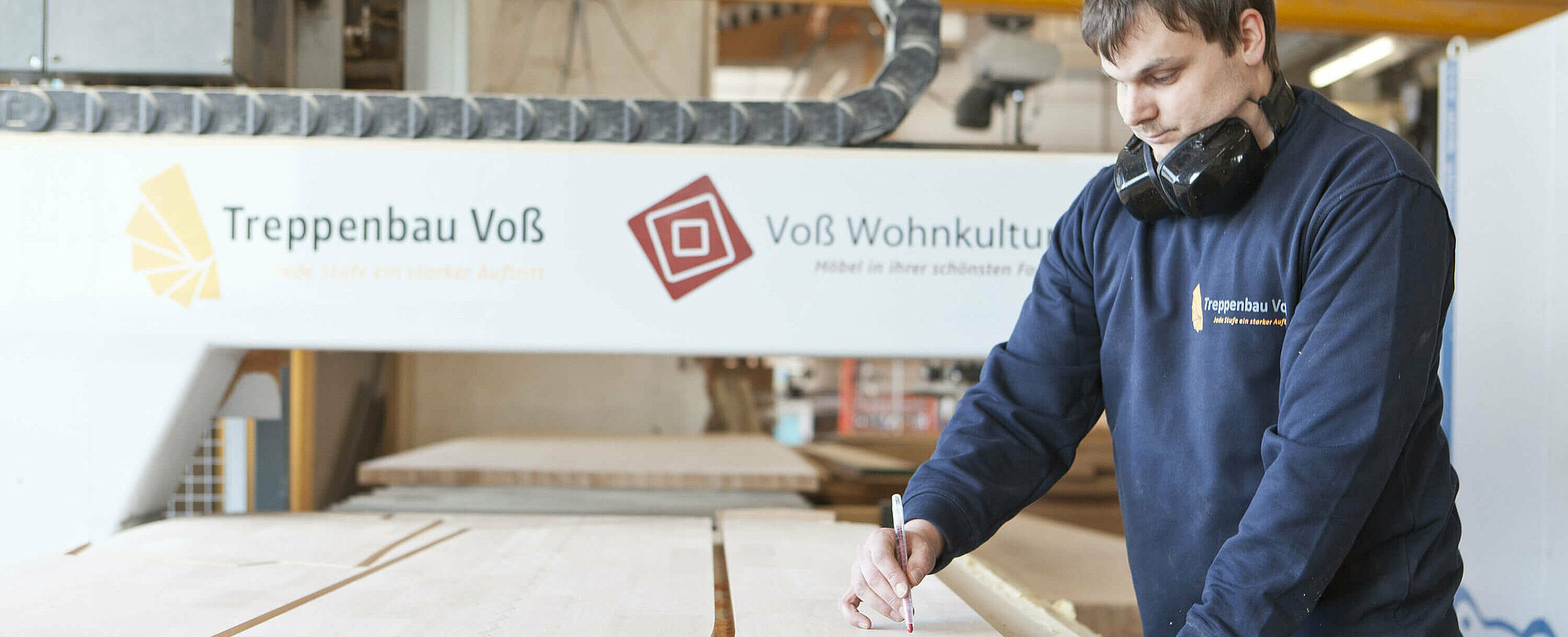
© Treppenbau Voß GmbH & Co. KG
Plate Optimisation 2.0 in the Field
“Our optimisation has improved a lot since we have replaced our old software with the Compass Software module,” asserts production manager Bastian Groth. The stair builder is now able to include more diverse parts in the plate optimisation process and there are more options to process the parts and plates individually. Different parts that do not have to be processed with the grain can be turned any which way. The degree of optimisation can be increased even further by refining detail parameters or by increasing the calculation time. Intricacies like this may take a few more seconds during the calculation of the optimisation, but the precision and savings of material are that much greater. Before switching to the new module, the company achieved a plate utilisation rate of 72% by using a competing software, now they easily reach 80 – 83%. This saves money and the company is able to plan inventory more precisely.
Even though the module offers additional possibilities, which result in more diversity and flexibility, Mr. Groth estimates that the operation of the module is easier compared to the external software he was using previously. The entire stair building process is now conducted with only one software, the same one that controls the CNC machines in general, and all data is in one place. “Once we had set up all the predefinitions to fit our individual needs, the calculation only takes one click. The process is fast and easy,” Mr. Groth explains.
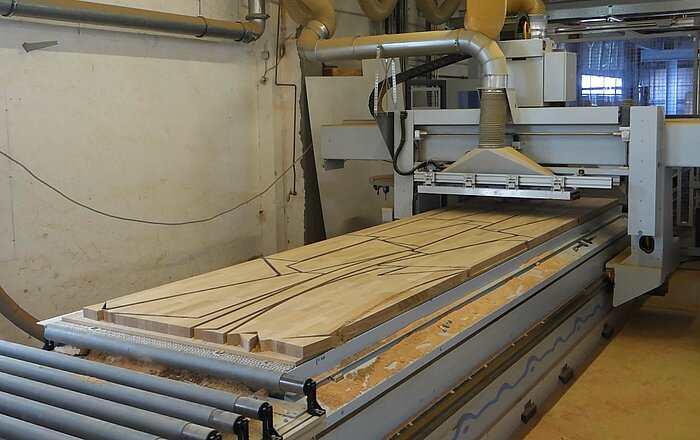
The software does not only allow for the optimisation of same parts on one plate, but also lets users mix parts. Furthermore, it is possible to determine, whether the grain is to be considered or not.
Moreover, optimised parts that can be processed right away, are milled completely within the same process. Other parts of the same optimisation that cannot be processed right away (e.g. because they require upright processing) are preformatted, that is they are milled with an excess, so that they can be processed further.
Since it is possible to mix both kinds of parts easily, it is possible to optimise more parts on one plate, which leads to a more optimal plate utilisation.
Treppenbau Voß combines treads, handrails, stringers, risers, ceiling paneling, and posts on the plates.
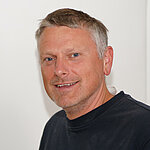
I can only recommend Compass Software. Personally, I have been working with the program for nearly 20 years. It is continuously being developed further and improved upon. The software’s scope is extremely wide when it comes to special cases, but it still covers all standard constructions for staircase building. I would say it is the best software in this field. The program is easy to understand and easy to use.
Bastian Groth - Production Manager
Compass Software: A Competent Partner
All in all Treppenbau Voß’s investment was a full success. “The biggest advantage is the savings of material due to the great utilisation of the plates. Beyond that the user-friendliness and simplicity is extremely helpful. Furthermore, I like Compass Software because they are always open to new developments and their implementation of programming requests is great,” Mr. Groth elaborates. During Treppenbau Voß’s frequent contact with the Compass Software Support Team, the two companies discuss further potential of the module, as well as possible new developments, which are implemented within a short period of time. “Since the module is brand new, we can discuss small details, which are important to us in the field, directly with the support team, who then forward them to the development department. This ensures a prompt programming of improvements and we are the first to benefit from them.”
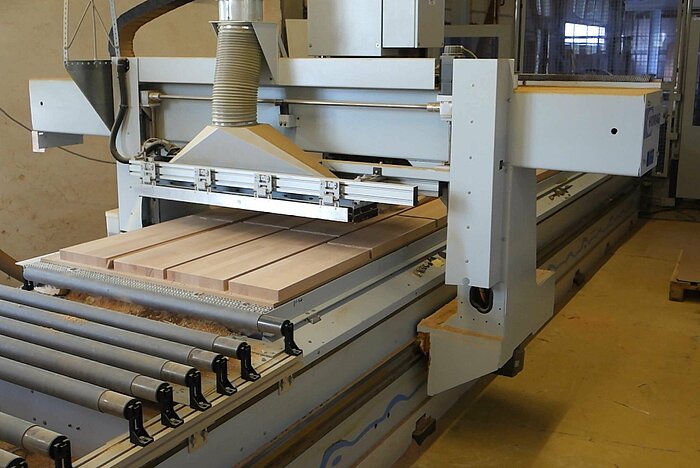
Treppenbau Voß will stick with their software partner Compass Software in the future and they already have new ideas for improvements and extensions which will make production run even more smoothly.
More Case Studies:
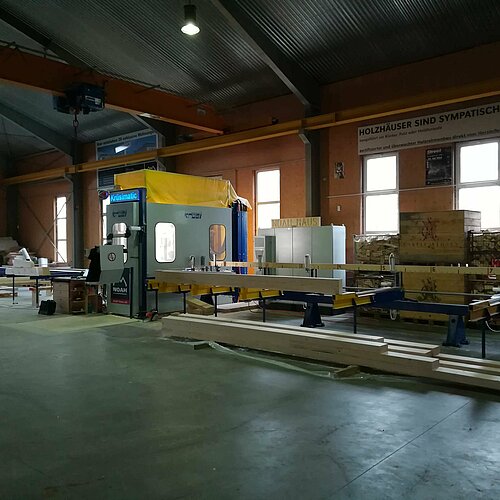
Automation of Production in Timber Construction - Noah Haus Implements Machine Manufacturing