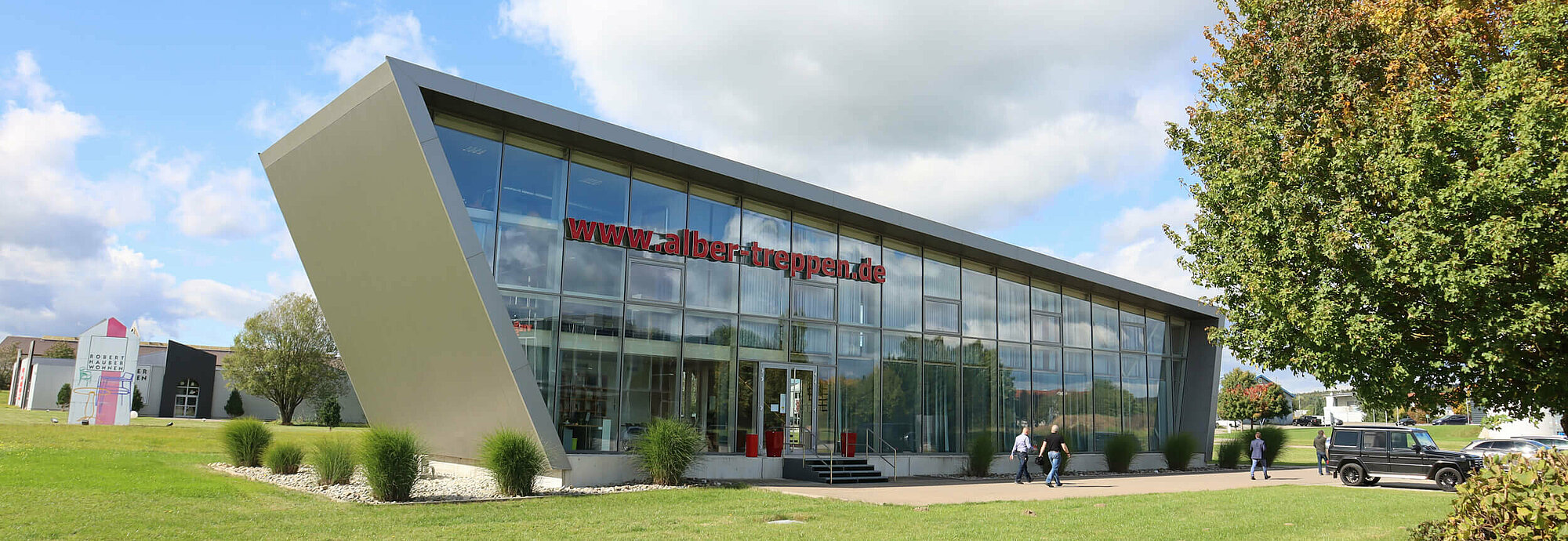
Alber Treppensysteme GmbH from Southern Germany has been using Compass Software´s powerful CAD/CAM solutions for nearly 30 years. In the beginning, Alber was still cutting wood manually with the help of 1:1 templates that were printed from the software on plotters. The stair builder bought his first 4 axis SCM CNC machine in 1995. Since then, the family business, which is currently run in the 2. generation, has grown extensively. The workshop´s stair output has increased almost tenfold in the last 15 years. Today, the stair builder owns two additional HOMAG 5 axis CNC machines and employs about 50 workers. Most of these developments happened during the last few years.
It was about 7 years ago when owner Juergen Alber realized that the only way he could continue to grow and stay competitive at the same time was extensive process optimization. Back then, Alber Stairs got more and more requests and their warehouse became too small. The stair builder had two employees who exclusively worked in the warehouse to organize and pre-cut wood plates. Individual stair orders were processed one after the other. The rising pressure for time made it more and more difficult to maintain this production method. Alber repeatedly tried to implement small optimizations, but he was missing an efficient and comprehensive production concept.
![Compass Software [Translate to Amerikanisch:] Juergen Alber utilizes Compass Softwares PROKON System](/fileadmin/_processed_/f/e/csm_Compass-Software-Alber_9_01_ba2b87c4b4.jpg)
You can read the entire case study in PDF format here:
![[Translate to Amerikanisch:] [Translate to Englisch:] Jürgen Alber](/fileadmin/_processed_/b/f/csm_Compass-Software-Alber_01_833f18aa21.jpg)
We visited several other stair builders back then to look at their warehouse solutions. Among these was also Meister Treppentechnik (another Compass Software customer) from whom we sometimes purchase treads. In the end, we discovered the warehouse solutions from the company Barbaric. Barbaric offers warehouse solutions that are built on a second level above the production floor.
Juergen Alber - Owner
PROKON: A Comprehensive Concept for Automated Processing
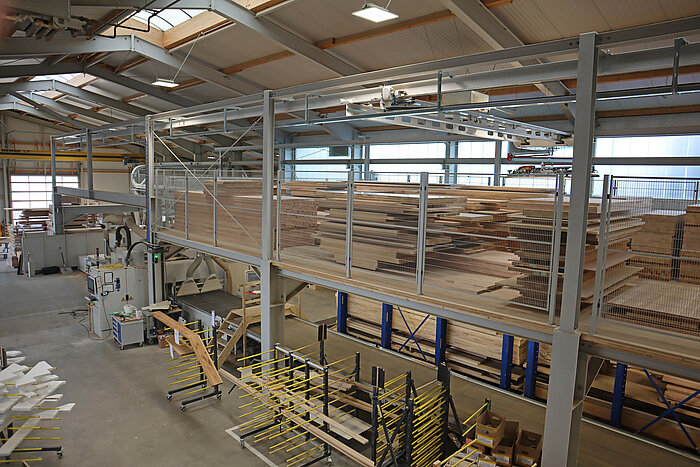
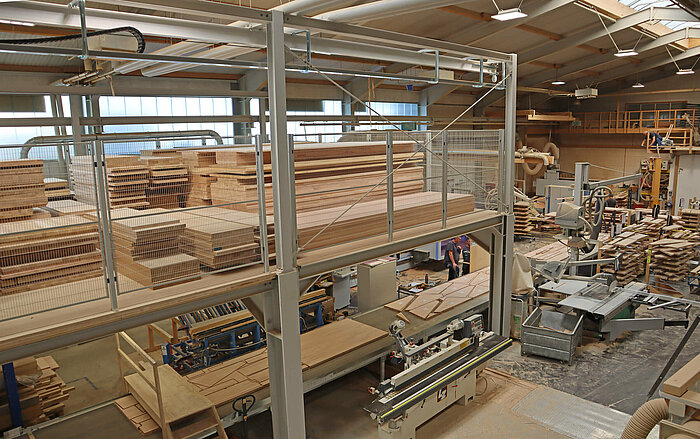
Compass Software´s decades long experience with stair building and the development of innovative technologies was the key element to success in the development of an encompassing production concept. An even closer relationship developed between the stair builder and the software developer. Alber communicated their needs and requirements for the software and Compass worked diligently on the best possible realisation of their wishes. Together, the companies brainstormed which elements to include in the comprehensive software concept. The software company operated as a consultant and partner. The best thing: all installation and developments were implemented at Alber Stairs during ongoing production, without creating any downtimes.
A warehouse such as this would mean that Alber could use their workshop space twice and would not have to build a separate structure. Next to the warehouse itself, Juergen Alber also wanted to optimize all production processes in his workshop. One of his top priorities was the automated loading of his machines and the digitalization of the entire production process. Unfortunately, there was no comprehensive solution for workshop optimization available on the market. Thus, Alber turned to Compass Software to develop a software concept for the production management and control of his processes. The final plan was devised in partnership with Barbaric, SCM, and Compass Software at the LIGNA 2019. The warehouse was to be constructed on a second level above the production floor and all processes were to be optimized with a new software solution developed by Compass Software. Compass was the glue that held everything together within this project.
Automatic Loading from the Warehouse through Nesting to the Finished Product
The second level warehouse has now been implemented at Alber Stairs. The floor space underneath can still be used as a normal workspace with few restrictions. Wood plates are now transported with a crane from the warehouse to a labelling station. There, the plates are automatically labelled with barcodes. The system autonomously calculates which spots will remain after nesting, so that the barcode labels will not be cut off.
Thanks to Compass Software´s Plate Optimisation 2.0 module, all plates are optimally filled with stair parts. Subsequently, the crane transports the plates along to the new SCM nesting machine with automatic vacuum cups. The CNC nesting machine already finishes all parts, if possible. Afterwards the components are automatically transported to different stations: to unloading stations for finished parts, to buffer or storage stations, or directly to the CNC machines for further processing.
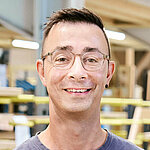
The old and new production processes are worlds apart. PROKON gives us the perfect overview at any time. It tells us where components are and what processes they still have to run through. Everything is shown on the monitor. We don´t have to go around asking questions. Everyone can get an overview quickly.
Franco Jengo - Production Manager
Complete Control Via PROKON
The ingenious highlight of the process: the entire production is controlled with the MES software. Alber Stairs maintains complete control and an overview at every point of production. It is no longer necessary to finish each project one after the other. Instead, the most efficient production flow is deployed. PROKON and barcodes make it possible to find any component at any time. Damaged or defective parts can be labelled via barcode by an employee and can be re-entered into the system for repair or new production.
Juergen Alber is thrilled: “The entire flow of information has been optimized. We don´t have to scramble for folders. Back in the day, everyone involved only had part of the project information. Everything was printed on paper. It´s easy to lose something or mix things up. Now, all of the production information is available to everyone digitally.”
Transparency and Honesty Leads to Happy Employees
Many things have changed at Alber Stairs since the implementation of PROKON. Just within the last year, the company grew from ca. 40 to 50 employees. Many workers have different jobs now and can be utilized more efficiently. Jurgen Alber emphasizes the importance of open communication and proper employee training during such an enormous change.
![[Translate to Amerikanisch:] [Translate to Englisch:] Jürgen Alber](/fileadmin/_processed_/b/f/csm_Compass-Software-Alber_01_b5b1ff20ed.jpg)
Of course, there were many uncertainties and much anxiety. An employee suddenly hears that their position will no longer be necessary. In such a case, it is important to be transparent from the start and to explain why the work processes are being changed and what the new role of the employee will be. You have to take the fear away from people and involve them. This way they accept change much better and enjoy being part of the process.
Juergen Alber - Owner
Security and a Significant Increase in Production since the Implementation of PROKON
Today, Alber Stairs produces significantly more than before PROKON. What is more, the stair builder has not even reached 100% capacity yet. One of the most highly valued new features is the clear component tracking that the MES solution offers. This creates security. The stair builder can see the status of each project at any time.
This is a huge advantage when it comes to commissioning. A missing component during assembly is a disaster. The workshop optimization nearly eliminates these occurrences. In general, the stair builder was able to reduce all mistakes by 2/3. The nesting leads to an additional savings in materials of 25% for some wood types.
![[Translate to Amerikanisch:] [Translate to Englisch:] Jürgen Alber](/fileadmin/_processed_/b/f/csm_Compass-Software-Alber_01_e4cd195e1d.jpg)
I always feel in very good hands with Compass. We have a great partnership, and the entire project is a clear win-win situation. This investment has definitely been worth it for me. I have been relying on Compass Software´s powerful CAD and CAM solutions for decades. Their developments are on a very high level. Compass remains true to their core, the stair software, but they have also realized that we will need additional software solutions in the future.
Juergen Alber - Owner
An Outlook into the Future
The next step at Alber is to optimize their work preparation processes so that they can keep up with the fast production. Juergen Alber knows he cannot be complacent: “It is imperative to always keep at it in this industry. Stair builders have to realize that new machine technology will not be the future. The most important thing will be process management and optimization. That is the only way we will be able to maintain the high-quality standards we have for German products and to keep wages high while competing with the rest of the world.”
Juergen Alber will recommend Compass Software to anyone who is interested in process optimization. PROKON makes the stair builders production future-proof. Thus, nothing stands in the way of Alber´s continued growth.
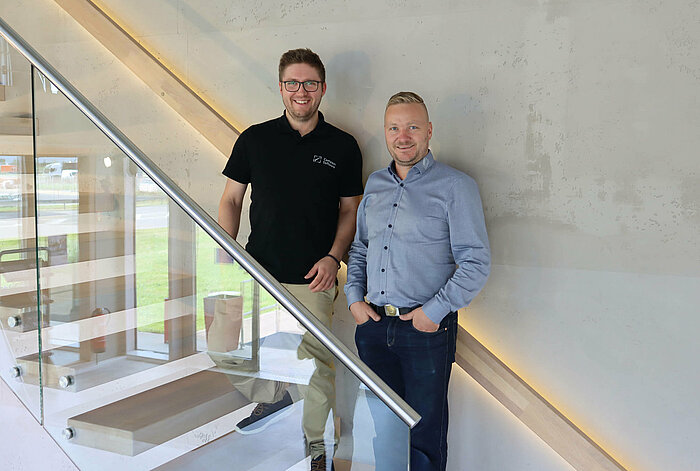