The modules save time, money, and create production security!
Have you seen our modules Barcode and Table Arrangement?
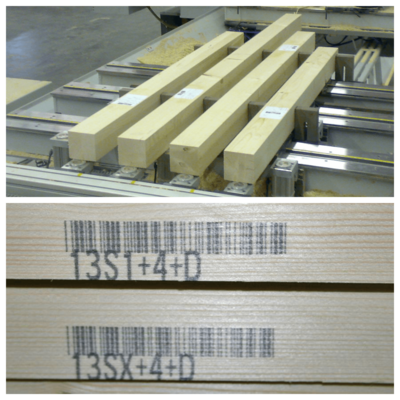
The modules save time, money, and create production security!
The module barcode is used whenever processes need to be automated. The function does not necessarily require the use of barcodes but can also be operated with RFID chips or manual input.
The reading of the barcode initiates the following executions on the CNC machine:
The utilisation of barcodes makes the operation of the machine extremely save. The CNC program is calculated just-in-time, so exactly at the time when it is actually needed. This reduces errors and creates security. For example, if a tool breaks during production, the newly generated CNC program will already include the new tool settings. This may not be the case, if the CNC program had been generated during job preparation before.
Furthermore, it is possible to print out barcodes on forms, which can be used in the following areas:
The module table arrangement makes it possible to position and process several components simultaneously on one machine table with optimised tool changes on suitable machines.
Since most machines require a lot of time for tool changes, this module significantly reduces processing times. For example, it would be possible to place 4 risers on one table. The machine would then go through each individual processing step (e.g., milling the contour) on each component, before it would switch over to the next processing step (e.g., drilling).
The modules barcode and table arrangement can be combined to achieve outstanding results. In this scenario, the machine stations will also be assigned a barcode. The machine operator scans the component (e.g., stringer, tread, post) and then the table station where the component will be placed.
The machine operator can decide freely where to place the parts. Afterwards the system will generate the CNC codes for all scanned components. The parts are processed with tool optimisation and optimised tool paths. This saves time and the machine operator can generate the CNC programs directly on the machine.
This solution is especially time saving for the processing of posts since several posts can be finished at the same time, including all optimisations.
You can read some practical examples on our website:
Case Study Luxholm Bauelemente
Barcode Application at Trappentoko
Barcode Application at Frammelsberger
Are these the features you have been looking for? If so, please contact us anytime: Sales