![Compass Software [Translate to Amerikanisch:] CPI Trappen](/fileadmin/_processed_/d/6/csm_Compass-Software-CPI-Trappen-1_095d54bb55.jpg)
CPI was founded just seven years ago by two partners in the Dutch city of Rotterdam to produce custom wood products, such as doors, windows, and creative designs on a modern CNC machine. The manufacturer started producing stairs as a service for other stair builders about three years ago. Next to their other products, the company produces about 5-6 stairs per week with only six employees, today. The manufacturer plans to double this number in the next 12 months.
![Compass Software [Translate to Amerikanisch:] CPI Trappen](/fileadmin/_processed_/9/6/csm_Compass-Software-CPI-Trappen-Dennis_993eacaf29.jpg)
Nesting without a Nesting Machine
CPI has developed a unique process for nesting parts on its 5-axis Holzher Pro Master 7225. This is done without the use of a specialized nesting machine and can be applied to any other standard 5-axis CNC machine as well. To do this, Dennis first optimizes different stair parts on a plate, using the Compass Software Plate Optimization 2.0 module. The software module guarantees the most optimal calculation of parts on the plate with minimal material waste. CPI saves about 20% of material with this feature.
Once the components are optimized on the plate, CPI begins its unique machining process. The machine table is loaded with a multi-use disposable plate. This plate is fastened on the machine with vacuum cups. The operator then uses a forklift to load the machine with the actual solid wood board. The plate is adjusted on the machine by using a laser to show the contours. The machine operator then fastens the solid wood plate to the disposable plate with regular screws so that it does not move during production. After starting the Compass Software CNC program, the machine nests the parts without manual intervention.
While the machine is running, the operator has time to remove parts from the previously finished plate and label them. The operator also has time to manually finish parts, if necessary.
We can return larger parts, such as stringers, to the machine individually for finishing with drillings, sanding, etc.
Dennis de Zeeuw - Owner
![[Translate to Amerikanisch:] CPI Trappen Dennis de Zeeuw](/fileadmin/_processed_/9/f/csm_Compass-Software-CPI-Trappen-Dennis-2_f759e42a6b.jpg)
One of the biggest benefits is that we save about one day a week of production time. We can produce more stairs with the same number of people.
Dennis de Zeeuw - Owner
Savings: 20% Production Time + 20% Material
The unique nesting process has several benefits for CPI: "One of the biggest benefits is that we save about one day a week of production time. We can produce more stairs with the same number of people," Dennis explains This is due to the streamlined machining of components and the time saved on individual tool changes. Before this process was implemented, an operator had to be constantly at the machine loading and unloading parts. This is no longer necessary because the machine can work independently for 45–60 minutes. The machine operator can use this time to finish parts and label them for shipping. CPI is using the extra production time to produce more stairs. Dennis is confident that they will double their production from 6 to 12 stairs per week in the next year.
Another major benefit is material savings. CPI saves about 20% of material by using the nesting method. Dennis explains: "The Compass Software plate optimization module automatically calculates all the parts on the plate, which reduces errors when cutting parts. We have seen a reduction in damage to our vacuum cups because they are protected by an extra plate and there is almost no chance of the tool running into them."
In addition, the double-plate operation allows the stair builder to optimize small parts on the machine, which would not be possible on a specialized nesting machine because the vacuum cups would not be able to hold such small parts.
![Compass Software [Translate to Amerikanisch:] [Translate to Englisch:] CPI Trappen Nesting](/fileadmin/_processed_/4/7/csm_Compass-Software-CPI-Trappen-2_443b5ab9f2.jpg)
![Compass Software [Translate to Amerikanisch:] [Translate to Englisch:] CPI Trappen](/fileadmin/_processed_/e/6/csm_Compass-Software-CPI-Trappen-3_6ad6dfa5c2.jpg)
Finally, the process makes the machine less physically demanding to operate. Previously, the machine operator had to constantly lift solid wood components on and off the machine. Now, the heavy solid wood panels can be loaded onto the machine with a forklift. After processing, the plate is slid onto a roller table that is the same height as the machine table. The components are already loose and can be taken out of the plate easily. This saves a lot of physical labor and effort.
Overall, Dennis is happy to be able to produce this way with Compass Software and sees great potential for the future.
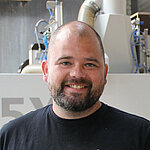
I am happy with the capabilities of the software and the technical support team. I would recommend Compass Software to anyone in a heartbeat.
Dennis de Zeeuw - Owner